Inkjet printing has over and over proven to be an important tool in research in the last few decades. As a digital deposition tool, tiny quantities of liquid can be placed in a controlled and reproducible manner. Moreover, due to its ability to pattern materials in an additive manner, inkjet printing can easily be integrated in a fabrication process, like roll-to-roll manufacturing.
As in many deposition methods there is a constant battle between resolution and throughput. Either printing at high velocity, like news paper printing, or printing at high resolution, like electrohydrodynamic printing with femtoliter droplets and resolutions down to single digit micrometers. Inkjet printing can be seen as a technique that is between these two extremes: printing velocities of several meters per second and a resolution down to 10 micrometers. Although much research was done in the last 10 to 15 years to narrow the line structures either by decreasing the nozzle size, or by altering the wetting properties of the substrate, or even by tailoring the ink properties, there is a difficulty to directly print with a resolution below 10 micrometers.
Prof. Timothy Singler and colleagues from the State University of New York have taken advantage of a hydrodynamic phenomenon called “evaporation-driven convective particle self-assembly” for high-resolution patterning. This method does not require the assistance of expensive and sophisticated printing systems. Also, no expensive substrate tailoring methods are required, just a simple oxygen plasma without additional chemical processes — hence limiting the chemical waste generated in whole process. Using this technique, the researchers are able to achieve nearly continuous change of the substrate wettability. For improving interfacial adhesion, the inherent properties of polydopamine were used. Such bio-functional materials can adhere to a broad range of materials effectively and, as a result, there is no need for specific surface chemistry or adhesion promoter during ink formulation.
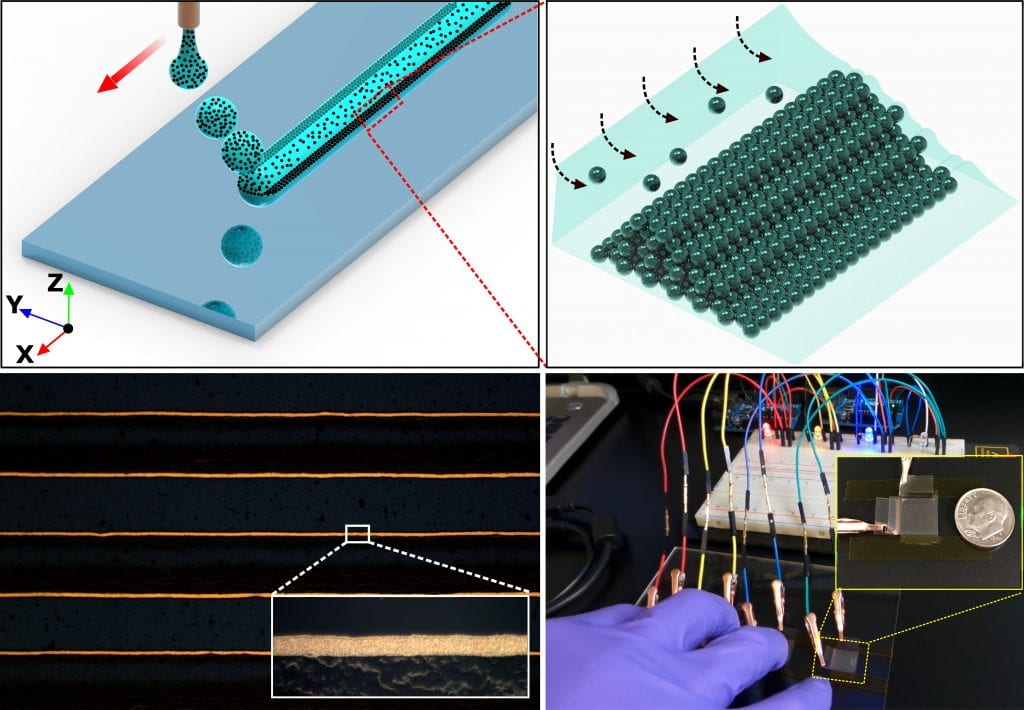
The impact of the research is trying to emphasize such an idea, that is, that additive manufacturing technologies would be facilitated with the alignment of all steps toward the low energy, materials, and environmental costs, not just the printing process itself. Such a broader picture needs to be kept in mind with careful design and selection of detailed processing techniques. The next challenge here would be to make the process suitable for large-scale manufacturing (e.g., roll-to-roll). The current plasma treatment is still a vacuum process, and the hydrophobic recovery subsequent to plasma takes a long time.
Liang Liu, the first author of the paper, says: “These results demonstrate the potential of this technique for low-cost transparent and flexible touch sensing applications in the near future.”
Reference: L. Liu et al., ‘Inkjet Printing Controllable Polydopamine Nanoparticle Line Array for Transparent and Flexible Touch‐Sensing Application‘, Advanced Engineering Materials (2020). DOI: 10.1002/adem.201901351