The capabilities of robotic systems has recently expanded into unstructured environments, which can include independent motion through rocky terrain, delicate object manipulation, or communicating and interacting with humans. Although the field has progressed significantly over the past few decades, there is still ample room for growth; for example, robots still fail to execute intricate or delicate tasks that are easily carried out by humans, and robotic engineering cannot yet mimic the intricate and synergistic characteristics of biological systems, such as our complex ability to perceive our environments through touch and smell.
Intrinsic or tightly integrated sensing, actuation, and computation embedded into 3D structures could enable a new generation of truly smart and complex systems, such as robots that have human-like dexterity, motor skills, and physical abilities that rely on feedback provided by the specialized receptors in the body. The field of robotics has strived to replicate these capabilities through flexible large area e-Skins, artificial muscles, and computing devices, etc. that are either placed on the external surface of the robot’s body or inside their rigid body to prevent devices from getting damaged during operation.
Various touch sensors and e-skins developed for robots today, including those mimicking some human skin features, such as fingerprints and increasing the tactile pixel (taxel) resolution, are developed on top of flexible and soft substrates to allow only their conformal placing on the outer surface of the body. This, however, comes with the challenge of wear and tear during frequent use.
In a recent study published in Advanced Intelligent Systems, Professor Ravinder Dahiya and his team at the University of Glasgow have demonstrated a new method to address the above issues by embedding the touch sensors in the distal phalanges of a robotic hand that is robust, stable, and affordable.
The robotic hand developed by the researchers is fabricated using 3D printing with the actuation system encapsulated in the core of the palm area, along with 3D-printed capacitive pressure sensors and readout circuit embedded in the distal phalanges of the fingers. This was achieved by modifying a fused deposition modeling 3D printer system to incorporate a paste-extrusion mechanism for simultaneous printing of structural polymers and conductive inks. This allows for the printing of functional robotic/prosthetic hands with embedded sensors at the fingertips to detect pressure.
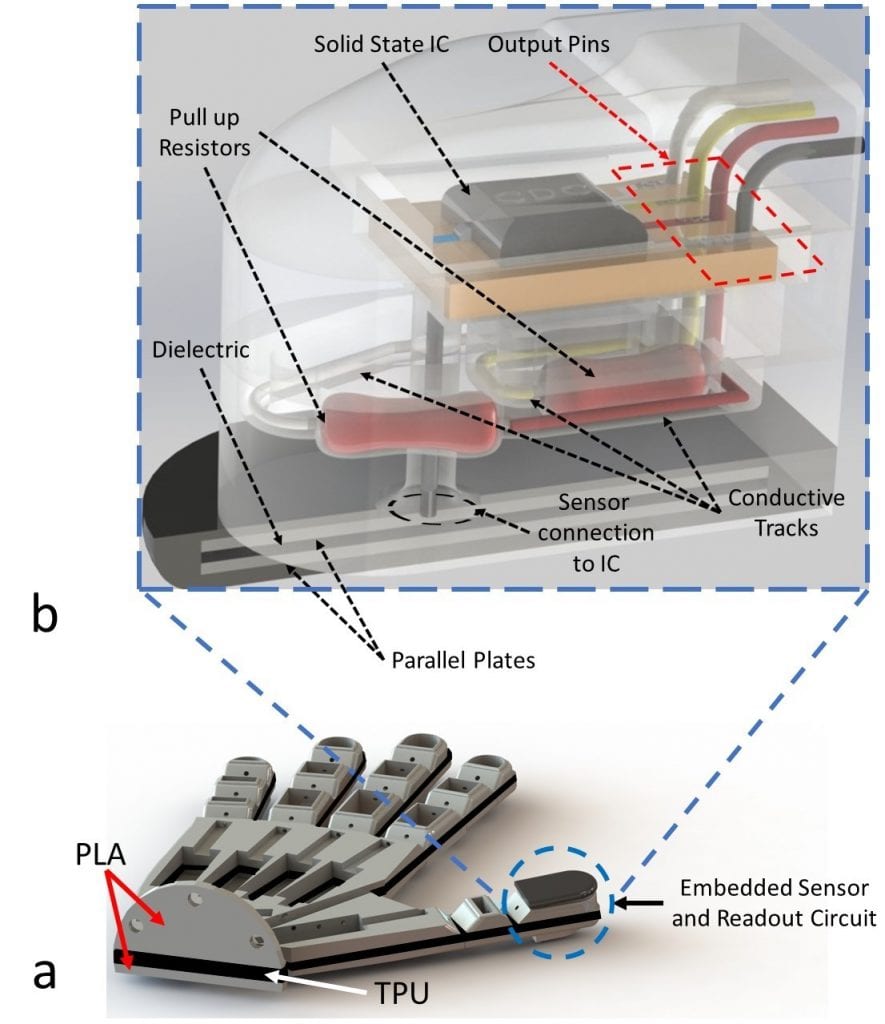
“The tightly integrated sensing elements within the 3D printed structures could pave the way for a new generation of truly smart material systems,” says Professor Dahiya, director of Electronic Systems Design Centre and leader of Bendable Electronics and Sensing Technologies (BEST) group at the University of Glasgow.
In the study, a combination of three conductive materials, namely a conductive carbon black polyactic acid composite filament, adhesive silver paste, and an in-house formulated graphite-based ink, were tested as electrodes for the capacitive sensors along with two dielectric materials: a flexible TPU filament and a two-part silicone rubber. The highest performing sensor was composed of the silver paste and soft rubber, offering a sensitivity of 0.002115 kPa-1 in the pressure range of 0kPa-50kPa.
The 3D-printed hand with embedded soft pressure sensing is an interesting approach for obtaining complex smart structures. The simplicity of the fabrication process introduces a cost-effective alternative fabrication method for tactile sensing systems that would otherwise require complex, expensive, and specialized equipment.
In this regard, compared to the state-of-the-art robotic or prosthetic hands, the presented approach could lead to robust and affordable hands with more functionalities. Further, the multi-material 3D-printing methodology offers a new outlook on the fabrication of robotics where embedded sensing capabilities can be achieved in a novel approach, providing efficient use of 3D space for embedded components.
*Kindly contributed by the authors.