Soft robotics are designed to emulate the complex motions of living creatures. Made of robust but compliant materials, they are more adaptable to their environment and present a lower risk of damaging the things and people they interact with than their hard counterparts.
Significant investment in their materials design and fabrication has seen soft robots establish themselves in more delicate fields such as healthcare (including surgical tools and assistants, prostheses, and other wearable technologies) and for exploration and surveillance in places where it wasn’t previously possible. The sticking point for moving these technologies forward has been their level of complexity: they are multi-component systems made of many different materials arranged into complicated geometries, requiring expensive multi-step manufacturing and external control systems to co-ordinate motion.
Rather than the standard cast-moulding with silicone, researchers are turning to 3D printing for a solution. “With 3D printing, complexity is free – it takes about as much time and energy to print a solid block of material as it does to print our robots,” says Michael Tolley, director of the Bioinspired Robotics and Design Lab at the University of California San Diego. “The challenge is generating the complex designs.”
3D printed pneumatic circuits now developed by Tolley, Yichen Zhai, and co-workers at UCSD and BASF don’t require any manual post-processing assembly. Unlike previous attempts to leverage such techniques, their robot can be manufactured in a single step, using nothing more than a desktop 3D printer.
The key lies in the design of their pneumatic valve system.
“A key achievement was designing this valve so it could be printed in a neutral state (no channels kinked, which would cause them to fuse shut),” the researchers explain. “When pressurized, the valve initialized itself (self-primed) into a part of its cycle (with some valves closed), before it began to oscillate.”
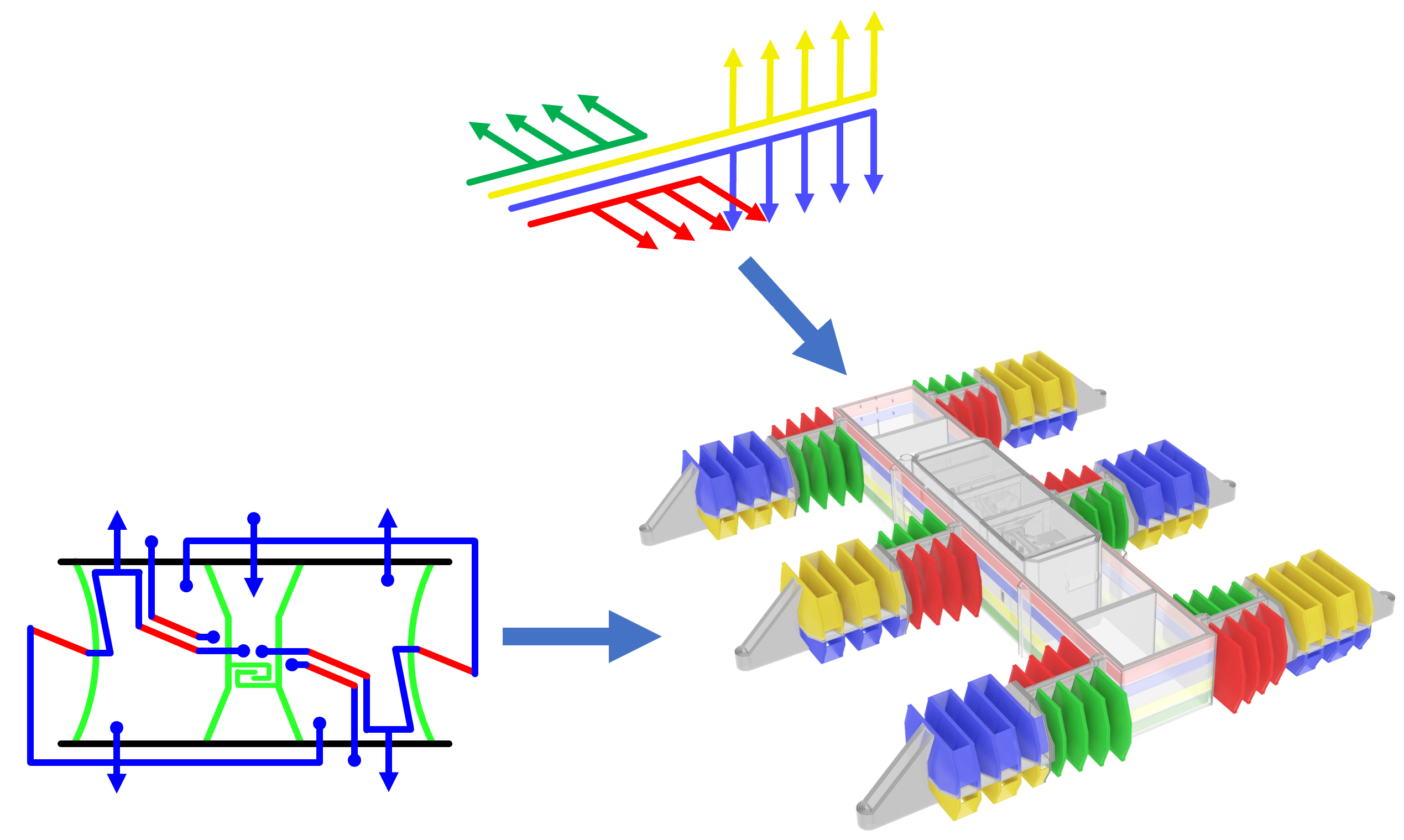
Cheaper, simpler production is already a huge advantage, but their new design has resolved another problem, too.
Because previous pneumatic systems relied on single, bistable valves or a three-phase ring oscillator as a control unit, the resulting phase shifts were asymmetric, leading to an awkward and inefficient gait and severely limiting the practical application of the robots. The new design produces symmetric phase shifts by generating four cyclic output signals from one constant pressure input. “We designed it to be very robust to different input pressures,” says Tolley, “to work with a variety of air-powered muscles and to handle different applied loads. This makes it ideal for controlling walking gaits.”
They demonstrated this stable, autonomous motion with a sig-legged robot. The single printing step to produce it, which they tested on different 3D printer models, took about 58 hours; thereafter, they used a 16 g CO2 cartridge with a mechanical regulator at 20 psi to power their pneumatic circuit and the robot managed to climb 73 cm up an uneven hill in just 30 seconds.
Using pressurised gas also offers the advantage that these soft robots can operate in places where electronics would require complex protection and shielding. Future directions may involve printable gas containers and the integration of mechanisms for responsive steering. With such developments, perhaps robots won’t just be walking on air – they’ll be driving and flying on it.
Featured Image Credit: David Baillot/University of California San Diego