For most of us, the word ultrasound is associated first and foremost with medical imaging and diagnostics. However, the high-frequency sound waves that form the basis of ultrasound imaging have found a number of other uses in the medical, scientific, and industrial domains.
One of the most important industrial applications is ultrasonic welding, a simple process for joining metals and plastics that requires no additional joining materials and is easy to automate. Ultrasonic welding involves only localized heating in and around the welding zone, and the maximum temperature reached is lower than for other common joining methods such as soldering or brazing. This last feature was the inspiration for a project at Imperial College London to explore potential applications in the field of plastic electronics where circuits are manufactured on low-cost, flexible polymer layers that cannot withstand high-temperature processing. The initial findings of this research are reported in a recent article published in Applied Engineering Materials.
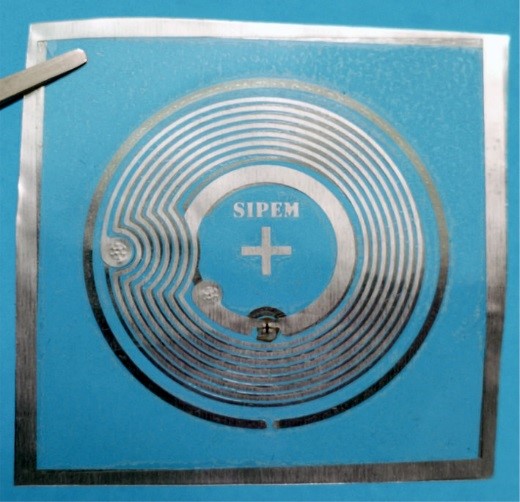
Plastic electronics is still at an early stage of development, and the focus up to now has been on improving individual components and building relatively simple systems that can demonstrate the future potential of the technology. However, things are moving quickly and soon there will be pressure to build more complex systems with greater functionality.
This will require novel approaches to assembly that are cheap, reliable and scalable to high production volumes. The production volume and unit cost projections for some of the products targeted by the plastic electronics industry are extreme. For example, it has been predicted that the demand for electronic product labels and security tags could reach 1 trillion units per annum and to be commercially viable these items will need to be manufactured at a cost of 1 cent or less. There are concerns that current assembly methods, which are based on electrically conductive adhesives, will be too expensive to meet this challenge.
The initial study at Imperial College has focused on building multi-layer, flexible circuits in which the connections between circuit layers are made by ultrasonic welding. Each layer in the circuit consists of a thin polymer sheet with a patterned layer of aluminium or silver on one side. Two distinct ultrasonic welding regimes have been observed depending on the process conditions. In the first regime, the metal layers are ruptured, and plastic welding occurs where the polymer sheets come into contact.
This results in a strong, multi-site plastic weld that holds the metal layers around the welding sites in contact, providing an electrical connection. In the second, less aggressive regime, the metal layers remain intact and a metal-metal weld is formed between them. Both types of welding are potentially significant for plastic electronics manufacturing. Type 1 welding can produce robust multi-level circuits, while Type 2 provides a possible solution for attachment of flexible integrated circuits which are likely to be too delicate for the Type 1 process. In both cases there should be advantages over adhesive-based methods in terms of both cost and reliability.
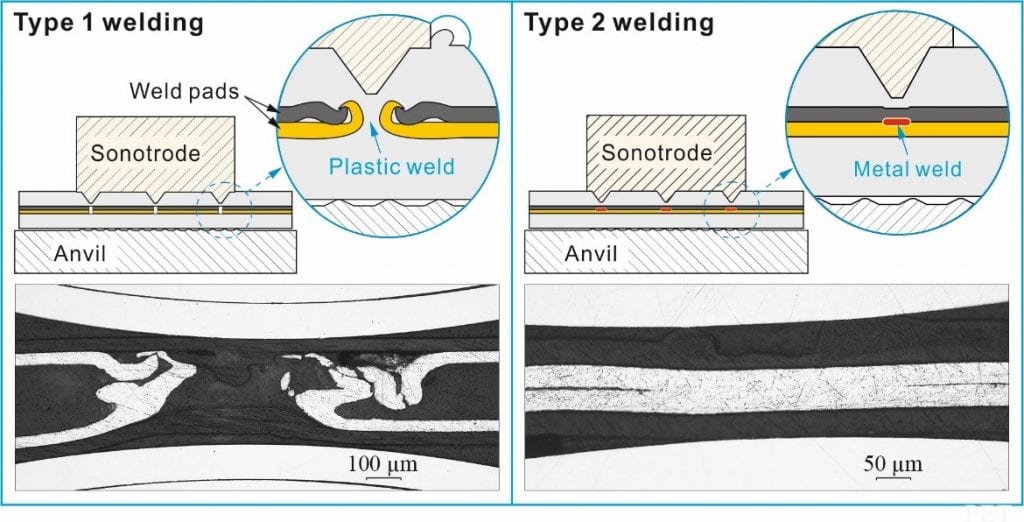
A limitation of ultrasonic welding as implemented in the Imperial College study is that welds are formed one-at-a-time in a serial process. However, this is not a fundamental issue since, with an appropriately designed sonotrode and the right ultrasound source, ultrasonic energy can be delivered simultaneously to many welding sites. The limits on this scalability, as well as the lower limit on the size of individual spot welds, still need to be established, and we intend to investigate these aspects in future work. We are also keen to find industrial partners to help us bring this technology out of the research lab and into production.
Reference: Guangbin Dou, Andrew S. Holmes, “System integration for plastic electronics using room temperature ultrasonic welding” Advanced Engineering Materials (2020). DOI: 10.1002/adem.201901309