Natural materials with outstanding mechanical properties exhibit at the micro-/nanoscopic scale common patterns that are pervasive across different living species. In the long for reproducing what Nature has already perfected, a most appealing pattern is the helicoid motif as it provides enhanced fracture toughness and damage resistance. The architecture of this class of patterns composed of regularly stacked fibrous layers (Figure 1a) is the origin of its high adaptability: a change in the pitch rotation angle between fibers (γ, Figure 1a) is reflected by a change in the mechanical response of the material.
In a recent study, Prof. Espinosa and collaborators demonstrated the adaptive behavior of helicoidal architecture in nature by performing a mechanistic analysis of changes in the exoskeleton structure of a figeater beetle (Cotinis mutabilis) at different stages of the animal lifetime. To complement the understanding of the helicoidal architecture as a highly adaptable system, synthetic helicoids were then reproduced by 3D printing technology and studied for a systematic analysis of the mechanics of deformation and fracture.
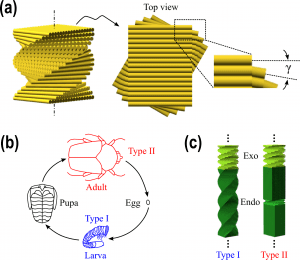
Figure 1. a) Schematic representation of the helicoidal architecture. b) Schematic of the typical life cycle of the figeater beetle with the different animal morphologies as it transitions from egg to adult. c) Schematic showing the helicoidal structures of the exo- and endocuticles in the figeater beetle at the larva stage (Type I) and at the adult stage (Type II).
The figeater beetle exoskeleton (or cuticle) and the development of its helicoid motif were examined at two different developmental stages, that is, the larva and the adult stages (Figure 1b). A specific aspect of the cuticle architecture that is modulated during the developmental stages is the organization of fibers in the exo- and endocuticle layers. At the larva stage, the exo- and endocuticles are distinct helicoidal structures with different pitch angles (Type I, Figure 1c). At the adult stage, the exocuticle layer features the same helicoidal structure as that of the larva; however, the endocuticle structure transitions from a helicoidal to a pseudo-orthogonal architecture composed of alternating layers of orthogonally aligned fibers separated by a thin helicoidal transition zone (Type II, Figure 1c). These changes in the exoskeleton architecture occur in response to a biological need: while in the larva stage the cuticle serve as protection against predation, in the adult beetle the mixed helicoid motif comply with a more complex functionality that balances protection (for the underlying wings) with flight mechanics (generating flapping forces during flight).
The same motif-functionality interlacing was reproduced in 3D printed synthetic helicoidal structures that were tested under uniaxial tensile loading. The mechanical response of these synthetic composites exhibited elasticity/inelasticity and failure that strongly depend on the pitch angle between layers. Analysis of the stress-strain data showed for example an overall enhanced toughness with reducing the pitch angle; moreover, smaller pitch angles resulted in fracture morphologies with more clearly defined helicoidal patterns (Figure 2).

Figure 2. Overview of the fractured surfaces in the synthetic helicoidal composites with different pitch angles: a) γ = 15°, b) γ = 60°, c) γ = 90°. For each pitch angle value, schematic of the fiber layup (left) and fractogram (right).
With that parallelism between Nature-optimized structures and synthetic architectures set, Prof. Espinosa concluded that as Nature achieves highly performing architectures through efficient selection and organization of building blocks, additive manufacturing can be also developed to achieve desired chemistry, functionality and mechanics by imparting to synthetic composites specific structural motifs. The authors suggest that the outcome of their research will pave the way for designing bioinspired adaptable fibrous composite systems that can eventually shed light on how Nature has evolved materials focusing on optimizing mechanical properties.