Polypropylene (PP) is a thermoplastic polymer with excellent chemical and mechanical properties such as rigidity, toughness, highly resistant to solvents and chemicals at moderate temperatures. It is currently one of the most used synthetic plastics in an exceptionally wide range of applications, ranging from textiles to laboratory equipment. The demand for PP with unique wettability and functionalities has grown exponentially due to the importance in many industrial and biological processes where self-cleaning, anti-bioadhesion, anti-icing/fogging or water/oil separation qualities of PP are needed. Currently, many different “bottom-up” and “top-down” techniques have been investigated to prepare superhydrophobic surfaces. Isotactic polypropylene (iPP) is the most used type of PP, but it exhibits low wettability: a quality that severely restricts the use of coatings for its chemical modification
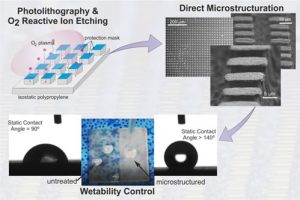
The researchers have fabricated hydrophobic isostatic PP surfaces with static contact angle above 140° by using a simple micro-structuration process based on a standard photolithography further oxygen plasma etching.
Wettability (hydrophilicity and hydrophobicity) can be tunable by changing surface chemistry; for instance, with a specific coating, or by structuring surface with a specific pattern to achieve complex roughness.
In Plasma Processes and Polymer‘s most recent issue a new study is published where Spanish researchers used a simple micro-structuration process on hydrophobic (isostatic) PP to improve the undesired wetting behaviour. The micro-structuration process is based on standard photolithography, oxygen plasma and thermal annealing. Durable and wear resistant polypropylene surfaces with static contact angle (SCA) above 140° have been fabricated using standard photolithographic process and O2 plasma etching followed by thermal annealing at 100 °C. This microfabrication process leads to a hierarchical topography derived from the patterned microstructures and the sub-micron roughness caused by plasma. This procedure could be adapted for the large scale manufacturing of plastic labels or films with functional properties and would be easy to integrate in countless everyday products.