Insects are social animals. A team of ants can collaboratively carry materials that are over 100 times their own weight and on hot summer days, honeybees line up in front of their beehive and synchronize their wing flapping to generate airflow in and out of the beehive, cooling the inside temperature.
Studying these collective behaviors could enable future robots to perform insect-like tasks, such as pollination. Over the past twenty years, microroboticists have studied how to build insect-scale robots.
Leveraging interesting physics at the small scale, scientists have built tiny robots with insect-like functions that are absent in larger scale robots, such as 1 cm long jumping robot that can reach a height over 40 times their size; small, quadrupedal robots that can tread across a water surface, climb walls, and ceilings; small, flying robots that can perch on leaves, shine light during flight, or even perform a body flip mid flight.
While these robots are impressive, they work in solo mainly due to the difficulty in fabrication and limitations on robot robustness. Traditionally, most microrobots involve tedious design and manual assembly, limiting them from operating in a swarm. Without a large number of them, small robots would have a hard time working on complex tasks.
With the goal of enabling insect-like swarm flight, researchers from MIT have proposed new design and fabrication methods that cut down on time and resources when it comes to producing these tiny, swarming robots.
Automated design and scalable fabrication via 3D-printing
Traditionally, microrobots are designed using commercial computer-aided-design (CAD) software that is generally tailored for designing and making larger scale robot components.
In microscale fabrication, the 3D components that make up microrobots consist of many 2D material layers. For example, a simple structure, such as the wing hinge, consists of nine material layers and the design patterns in these materials are all inter-related. When using commercial software, a designer needs to manually create design patterns for all nine layers. If one design parameter needs to be updated, then a researcher must manually modify all nine sketches, which can be time consuming and lead to design errors.
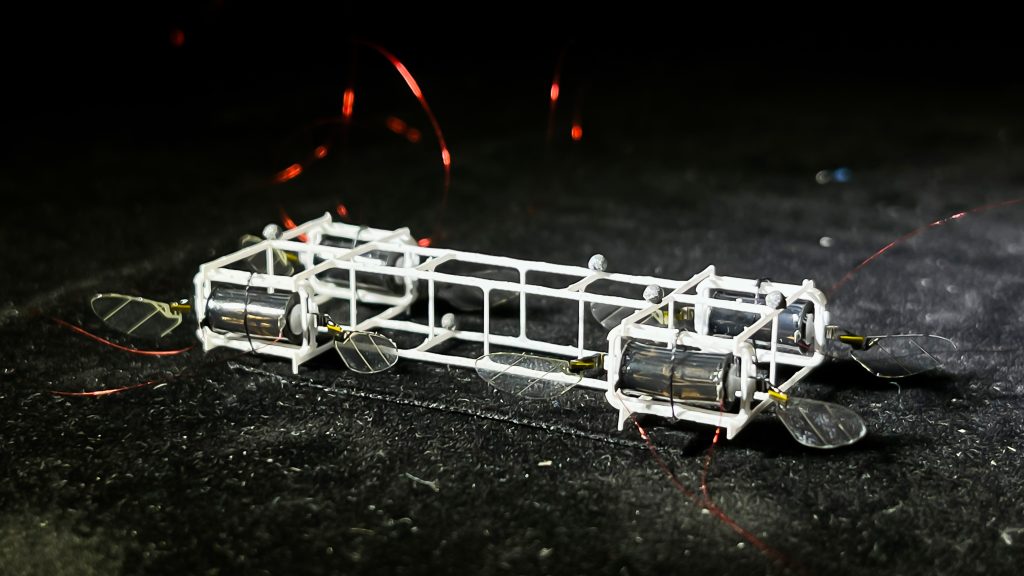
In a study recently published in Advanced Intelligent Systems, the MIT team developed a parametrized design approach where a researcher only needs to specify a few important parameters and then customized software generates all the necessary files. This design approach is tailored for microrobots, allowing focus on high-level designs and reducing design time from hours to within seconds.
This design approach was used in conjunction with 3D printing to automate fabrication. In the past, the airframes of robots developed by the team were made of 2D carbon fiber structures that required manual assembly under a microscope, which needed high skill and extensive training. In the study, for a single print job, components to build 64 robot modules were produced.
Coordinated flight of robotic insects
The robots in the current study resemble honeybees, flapping their tiny wings 400 times a second to get themselves off the ground. Compared to prior robots from the same research team, these robots with 3D-printed parts exhibited higher consistency in their ability to fly without extensive hardware and software tuning.
Collective transport of payload is especially important for tiny aerial robots. While one robot alone has a very limited payload, they may collectively carry heavier and larger objects. The coordinated flight of two robots flying in tandem was demonstrated in the study, and more impressively, they could fly together while carrying a long object.
In future, tiny robots could be deployed to collectively construct structures in cluttered environments, such as building a beehive on a tree branch. Alternatively, they may be used to remove dangerous materials from a site that larger robots cannot easily get in.
Despite having demonstrated the first coordinated flight in insect-scale robots — those weighing less than a paper clip — there is a long way to go before insect-like collaboration can be achieved in a swarm.
Insect collaboration seems spontaneous, they make individual decisions by communicating with their neighbors. Without a central commander, the insect swarm can collectively accomplish amazingly complex tasks, such as building hives or fending off predators. Insect swarm behaviors allow tens, hundreds, or even thousands of individuals to work together.
The team is eager to explore swarm algorithms and apply them to a larger number of their robots. In this process, new challenges will arise. For instance, when a larger number of robots fly in a small space, they would frequently bump into each other during flight.
The researchers are studying in-flight collisions and they are developing flight recovery controllers. They hope one day a small team of their robots can collectively pollinate flowers.
Reference: Yufeng Chen, et al., Modular and Scalable Fabrication of Insect-Scale Aerial Robots toward Demonstrating Swarm Flights, Advanced Intelligent Systems (2023). DOI: 10.1002/aisy.202300059