The body’s joints are among the most difficult parts to fully recover after injury. For instance, musculoskeletal disorders, fractures and dislocations can all be cause of dysfunctions to our body joints, leading, in the worst cases, to severe loss of mobility. When any of these situations occurs, an early diagnosis and an effective joint monitoring can determine the resolution of any therapeutic treatment.
Indeed, monitoring joint movement is critical for many rehabilitation regimens, as well as improving sports performance. However, traditional methods of recording movement based on inertial measurement units (IMUs) are limited. For example, inertial sensors poorly locate specific joint positions, and camera systems are costly, immobile, and require extensive training to set up and operate.
Nowadays, flexible wearable electronics are a good alternative to IMUs but most demonstrations to date suffer from trade-offs, such as poor conformability to curved surfaces, expensive manufacturing, and difficult integration. As a consequence, these strategies can fail when applied to complex surfaces and complicated structures, such as joints. In this regard, the shoulder, one of the most mobile and complex joints in the human body, is notoriously difficult to track because of its many degrees of freedom.
In light of this, Prof. Max Shtein and his collaborators have dedicated their studies to overcome the current issues of IMUs-based monitoring devices. In their article recently published in Advanced Materials Technologies, they have presented a new, wearable sensor patch for monitoring body joints.
Prof. Shtein, who has personally experienced the inconvenience of collarbone injury, has realized the importance of having a device that is able to follow the contour of complex joints in their wide range-of-motion.
Taking inspiration from Kirigami, the ancient Japanese art of cutting paper, Shtein’s group at the University of Michigan, USA, explored the effects of different rotational symmetries of cut patterns and their interactions with different 3D shapes. This study has ultimately led to the fabrication of a wearable sensor patch which can conformally follow the contour of the shoulder joint throughout its entire range of motion.
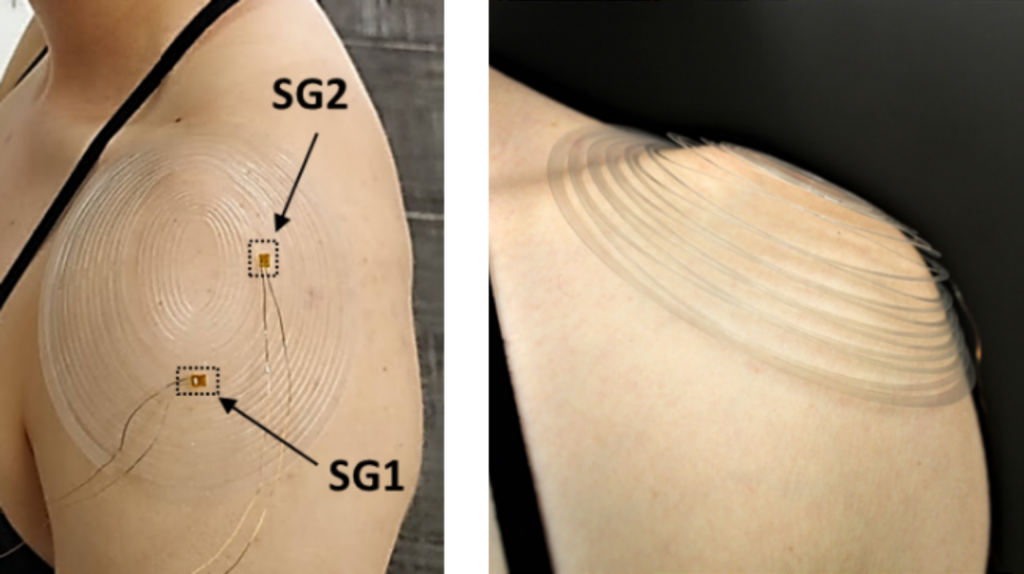
The sensor measures microscopic strain distribution along the kirigami structure. Small strain gauges, placed in the right locations along the patch, are able to monitor changes to the overall curvature of the surface. As a result, changes in the electrical signals from the strain gauges from movement allow the differentiation between various types of motion (e.g., running, shrugging shoulders, arm raises, etc.) in real time.
Beside the ability of effectively monitoring shoulder joint movement, the greatest advantage of the patch lies in its own structure: kirigami allows scalable manufacturing processes to be used. At the same time, its simple shape, flexibility, and ability to easily conform to a number of 3D shapes without wrinkling makes integration with textiles easier.
This promising study opens the door to new horizons of wearable fitness activity trackers and health-monitoring devices, ranging from charting athletic performance to detecting cardiovascular conditions. “Having cost-effective and reliable joint sensors could revolutionize physical therapy, coaching, gaming, [and] prosthetic control,” Shtein said. “To get there, we need to build on the present work.”
The challenges and the ambitions for this group of researchers do not end here. The team aims to obtain more portable and wireless sensor patches, enabling higher fidelity mapping of movement and better integrations into garments. We are waiting for the next step and look forward to their other successful advancements in wearable electronics!