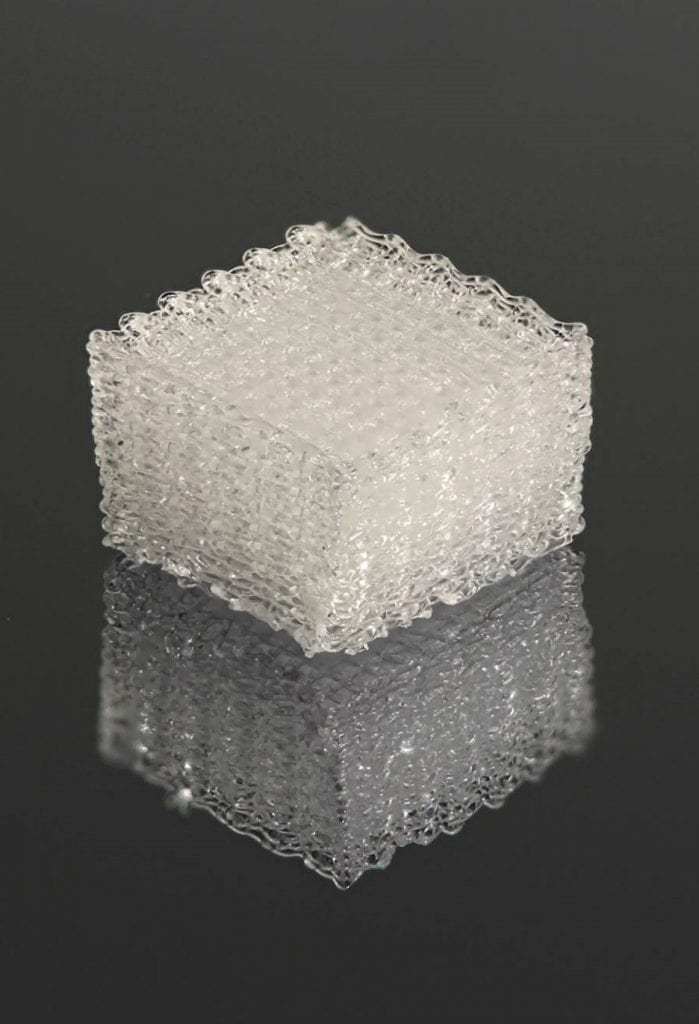
3D-printed glass woodpile scaffold, highlighting gap-spanning features.
In new work published in Advanced Materials, researchers at Lawrence Livermore National Laboratory have successfully 3D printed transparent glass using a two-step method that shows promise for the creation of glass optics as well as intricate glass structures.
In this work, special pastes are formulated, which contain silica particles suspended in a liquid which and can be squeezed into filaments that hold their shape, much like toothpaste from a tube. To build the desired 3D structure, filaments of the silica paste are formed and deposited in a highly-controlled manner using a 3D-printing process known as direct ink writing, commonly used to print plastics or ceramics. The structures are then heated, causing the particles to merge and form transparent silica glass.
This two-step approach enables the formation of a variety of glass structures, ranging from completely solid components that both look and behave like window glass, to open mesh structures built from fine glass fibers just over the width of a human hair.
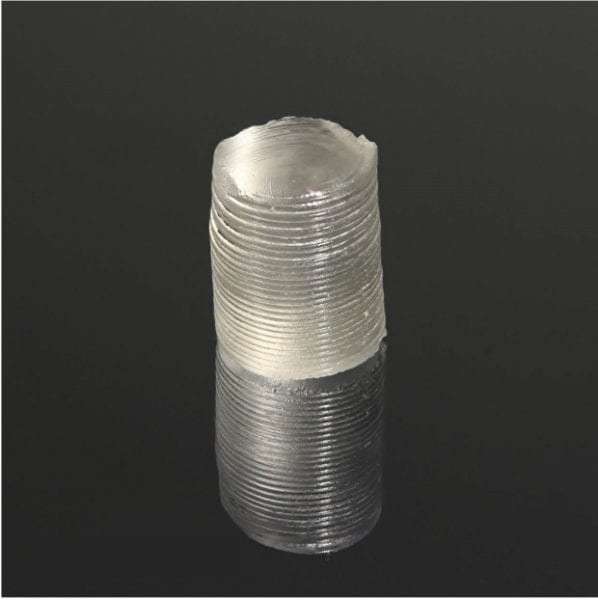
Solid, monolithic 3D-printed glass cylinder.
The research proves formation of transparent glass can now be accomplished with a high degree of 3D structural precision. In addition, the ability to produce glass using the 3D-printing technique opens the door to the possibility of creating new glass components that contain both compositional and structural gradients, enabling glass microfluidic devices with new functionality, as well as new types of gradient-index optics that can be made flat, saving money and time on polishing and finishing.
This work was performed under the auspices of the U.S. Department of Energy by Lawrence Livermore National Laboratory under Contract DE-AC52-07NA27344. LLNL-ABS-728603.
This article was kindly contributed by the corresponding author of the work, Rebecca Jeanne Dylla-Spears.