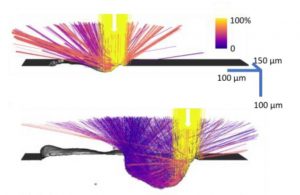
Laser rays and melt pool geometries from laser tracing simulation.
The 3D printing technology known as Laser Powder Bed Fusion (LPBF) additive manufacturing is becoming popular for manufacturing high-end specialized metal components. In order to fabricate parts with low porosity, controlled microstructure and low residual stress, it is fundamentally important to understand and control the thermal history during the LPBF process. Laser absorptivity, one of the key parameters in the laser-material interaction, is traditionally assumed to be constant in additive manufacturing (AM) modeling. In reality, it changes due to the surface morphology and temperature variation and is affected by multiple material properties and laser processing parameters.
This research, published recently in Advanced Engineering Materials, has filled a gap that has existed in quantitative characterization of laser absorptivity under real AM conditions and has established useful scaling relationships for process optimization. Previously, absorptivity was measured by either integrating sphere reflectometer or macro calorimetry methods. The former method involves not only the energy absorbed by the material, but also the energy loss due to evaporation and plasma absorption that is less important to the manufactured part properties. The latter macro calorimetry method uses large laser beam and low laser power density for absorptivity measurement, which is far away from real AM conditions.
In this work, the micro calorimetry method developed in LLNL’S Laser-Material Interaction (LMI) group was used to extract net material absorptivity under LPBF processing conditions for three important structural alloys: Ti-6Al-4V, stainless steel 316L, and Inconel 625. Finite element modeling was performed using a ray-tracing code, resulting in excellent agreement with the experiment. A set of universal scaling relations were also established that relate absorptivity and melt pool depth to material and laser parameters.
Modeling groups can now confidently include accurate energy coupling parameters, leaving less to guess work and improving the fidelity of their predictions. In terms of next challenges, the authors acknowledge that the derived scaling behavior may not work well for high thermal conductivity and low absorption materials, such as copper, aluminum, and gold. These materials are currently being studied with the methods described in the paper, along with laser parameter modifications such as beam shape and temporal modulation.
As Dr. Manyalibo J. Matthews states, “This work paves the way to accurate thermal history predictions for metal 3D printing based on precise energy coupling measurements and simulations.”