The prominence of plastic pollution and issues surrounding plastic disposal and recycling continue to be a sore spot among environmentally conscious consumers.
The prevailing philosophy among consumers for decades — that we can use as much plastic as we desire as long as we recycle it — is coming to an end as we finally confront reality: most of our “recycled” plastic is actually carted away to landfills, despite our best intentions.
The new, enlightened wisdom is to consume with the assumption that nothing gets recycled.
With state- and country-wide single-use plastic bans coming into effect, some strides have been made with this assumption in mind. But making the plastics industry more environmentally friendly from the get-go is up to scientists and engineers.
The Harth Lab, a polymer chemistry group at the University of Houston, has come up with a “deceptively simple” way to do this. In a recent paper in Angewandte Chemie International Edition, they describe a new route to synthesize plastics that addresses several environmental issues, including recycling.
Plastics such as polyethylene can be tailored to have either a high or low degree of branching (low- and high-density polyethene, respectively) for different products, such as the shameful plastic shopping bag —which, more often than not, isn’t recycled.
Block copolymers, on the other hand, incorporate segments of both low and high branching and are valuable from a recycling point of view because they compatibilize immiscible polymer blends, allowing different types of plastic to be recycled together.
Building on well-established polymerization methods, the UH researchers have achieved “branching control” of block copolymers in a one-pot process that only requires one starting monomer, a palladium catalyst, and an inexpensive additive — aluminum chloride, a Lewis acid.
Their reaction uses terminal alkenes (1-alkenes) as monomers, which are readily available at low cost. These 1-alkenes are isomerized quickly into internal alkenes by adding aluminum chloride in the middle of the reaction, yielding block copolymers. The composition of the blocks can be tuned by altering the point at which the Lewis acid is added.
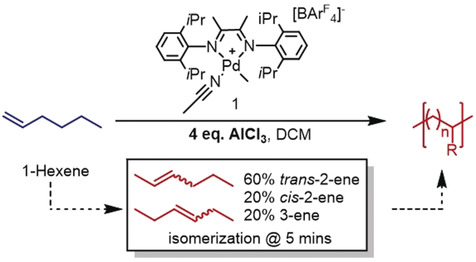
Aside from the recycling advantage, this method could also help us move away from coal, oil, and natural gas as monomer sources due to the versatility of the reaction, which also works for internal alkenes. For this reason, monomers derived from industrial waste streams and food sources are feasible.
Reference: H. E. Basbug Alhan et al. ‘Branching Regulation in Olefin Polymerization via Lewis Acid Triggered Isomerization of Monomers.’ Angewandte Chemie International Edition (2019). DOI: 10.1002/anie.201914742