There is a growing awareness in the climate debate that many commodity chemicals manufactured on the multi-million-tonne scale remain dependent on industrial processes developed around a hundred years ago. They are invariably energy and greenhouse gas intensive, and are no longer tenable in a sustainable society.
Perhaps the most visible of these large-scale processes are the syntheses of hydrocarbons, ammonia, urea, sulphuric acid, and hydrogen from the Fischer-Tropsch, Haber-Bosch, Bosch-Meiser, Contact process, and methane steam reforming methods, respectively. These familiar chemicals are used, for example, in the production of fertilizers, polymers, fuels, detergents, and pharmaceuticals.
A recent report has added the century-old Ostwald process for manufacturing nitric acid as a target for reform. More than 60 million metric tonnes are used every year to make dyes, pigments, nylon, and fertilizers. As well, the chemical is a key ingredient for making weapon-grade explosives.
The traditional reaction is energy intensive, fossil powered, requires high temperatures and pressures (800-950°C, 12 atmospheres), uses expensive and rare noble-metal-based heterogeneous catalysts, and carries a very large carbon dioxide and nitrous oxide greenhouse gas footprint.
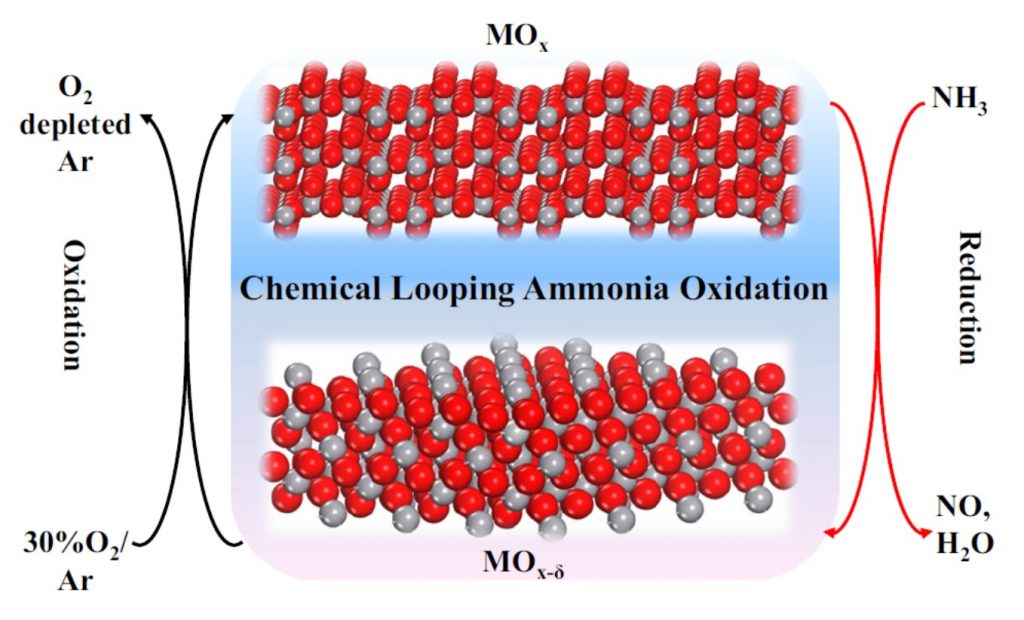
The new innovations circumvent many of the Ostwald process’ disadvantages. Rather than using a single-step reaction between ammonia (NH3) and oxygen (O2) to make nitric oxide (NO), the precursor to nitric acid (HNO3), the new process makes use of an innovative two-step, chemical looping reaction, illustrated in the figure, to yield a net reaction of 2NH3 + 3/2O2 → 2NO + 3H2O.
The reaction proceeds by first oxidizing NH3 to NO and water (H2O) using lattice oxygen from non-precious redox-active vanadium pentoxide (V2O5):
2x NH3 + V2O5 → 2x NO + 3x 3H2O + V2O5(1-x)
This creates non-stoichiometric V2O5(1-x) with lattice oxygen vacancies, which are then replenished with O2 to reconstitute stoichiometric V2O5:
V2O5(1-x) +5x/2 O2 → V2O5
This looping strategy enables an impressive NH3 conversion of 97% with 99.8% NO selectivity at a less extreme condition of 650°C and atmospheric pressure. In addition, the process boasts a lower CO2 footprint while reducing the selectivity of nitrous oxide (N2O) emissions to 0.1%.
With this victory, one can only imagine which timeless giant in the chemicals industry will be called next to the “green guillotine” of science’s sustainability revolution!
Written by Geoffery Ozin and Jessica Ye
Reference: Chongyan Ruan., et al., Selective catalytic oxidation of ammonia to nitric oxide via chemical looping, Nature Communications (2022). DOI: 10.1038/s41467-022-28370-0
Feature image credit: Crystal Kwok on Unsplash