Titanium, the ninth-most-abundant element in the earth’s crust, can be found in a wide range of everyday objects such as bikes, sports gear, technology, and even Apple’s new credit card.
As a structural metal, titanium is known for its excellent strength (close to that of iron) and significantly low density (twice as low as iron), finding applications in the aerospace and automotive industries. However, its widespread use is still far below competing metals such as steel and aluminum due to its economically and thermally expensive processing.
Given the limitations faced during the processing of titanium alloys, researchers at Florida International University have taken it upon themselves to uncover a fast and efficient processing route for titanium alloys requiring up to 50% less heat. The unprecedented low-temperature processing window reported not only has advantages in the processing of titanium alloys but also opens opportunities for future research investigating the fabrication of novel titanium-based composites.
The proposed processing route benefits from the simultaneously applied low temperatures (up to 650oC) and high pressures (up to 555 MPa) in spark plasma sintering (SPS) to achieve a fully dense part from an initial powder form. The authors attribute this striking finding to “high-pressure-assisted mass transport and induced plastic deformation mechanisms” during the processing of the alloy to result in parts with competitive mechanical and structural functionalities as compared to high-temperature-processed titanium alloys.
The team demonstrated that at low temperatures, the powder particles of the alloy experience stresses exceeding their plastic limit and promote their densification. The high levels of stress were evidenced in the form of deformation features unique to the alloy at the atomic scale using transmission electron microscopy techniques.
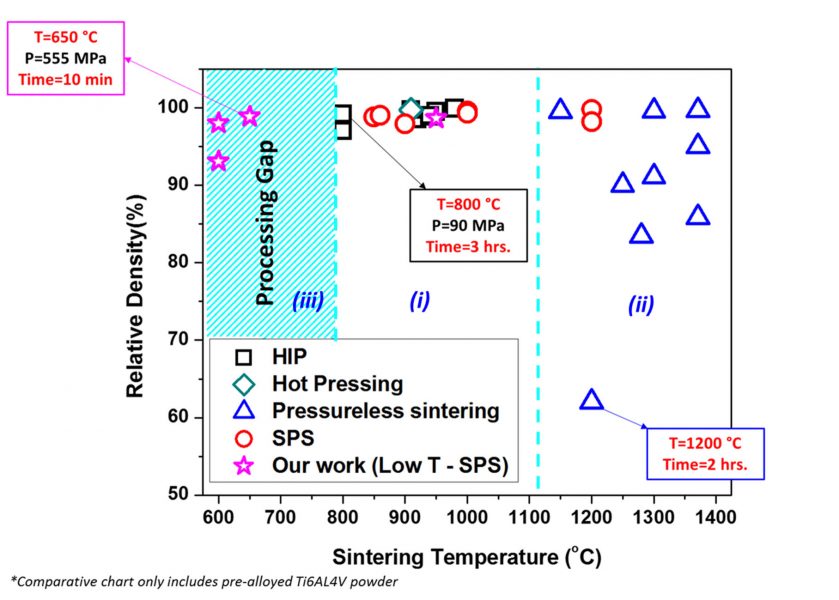
In titanium, atoms are closely packed in a hexagonal structure — the restricted movement of atoms in the crystal renders them with limited planes and directions in which deformation can easily occur. Thus, in the presence of compressive stresses like those experienced during processing, deformations are accommodated by the slip and arrangement of atoms across mirroring planes to generate twins. These unique features were found throughout the microstructure of the titanium processed at low-temperature regimes and are responsible for the excellent mechanical response.
Going forward, this technique offers an efficient alternative in the processing of titanium alloys by alleviating the exhaustive high-temperature schedules known to date. In addition, the research team considers the unprecedented low-temperature regimes to be beneficial in the processing of titanium matrix composites that were previously considered a challenge due to incompatible processing windows.
Written by: Arvind Agarwal
Reference: Jenniffer Bustillos et al. ‘ Ultralow Temperature Densification of a Titanium Alloy by Spark Plasma Sintering.’ Advanced Engineering Materials (2020). DOI: 10.1002/adem.202000076