Compared with conventional rigid robots with heavy metals and tethered motors, soft robots made from soft materials show promise by working intelligently just like biological organisms, since they possess more degrees of freedom in order to be dexterous and adaptive to environmental changes. However, their softness could also be problematic when it comes to sophisticated shape deformations or heavy duty work.
To precisely and locally control the shape and locomotion of soft robots with considerable strain and strength, actuators that are highly responsive and strong are required.
Among various soft and responsive materials, liquid crystal elastomers (LCEs) exhibit intrinsic anisotropy and reversible shape deformation during phase transitions upon exposure to external stimuli, including heat and light, which are highly desirable for actuators. By controlling the molecular alignment of liquid crystal molecules inside the network, the locomotion of LCEs can be preprogrammed. Nevertheless, the spatial control of alignment usually requires multi-step fabrications and limits the dimension of actuators. As elastomers, most LCE actuators also lack the desired mechanical strength to generate large amount of work.
Inspired by the musculoskeletal system in humans and other animals, our team led by Professor Shu Yang at the University of Pennsylvania has recently developed an extrusion-based method to fabricate meter-long LCE filament actuators.
To enhance the mechanical strength of the filament, up to 2 wt% carbon nanotubes, which are known for their ultra-high strength, low-weight, and high electrical and thermal conductivity, were added into the elastomers. Additionally, a small quantity of cellulose nanocrystals, a unique type of nanomaterial derived from plant cellulose fibers, were blended in to enhance the alignment of liquid crystal molecules within the filament, which is essential to achieve the anisotropic and reversible mechanical responses.
The ability of carbon nanotubes to absorb near-infrared light and release heat could trigger the phase transition in LCEs, leading to light responsive actuation of the filament. By combining copper wires with the filament, transferring electric current to heat, the hybrid LCE filament is electrothermally responsive as well.
Therefore, the filament actuator is dual-responsive, capable of fast and reversible actuation by application of either near-infrared light or a small voltage (8 V) as shown in the figure below.
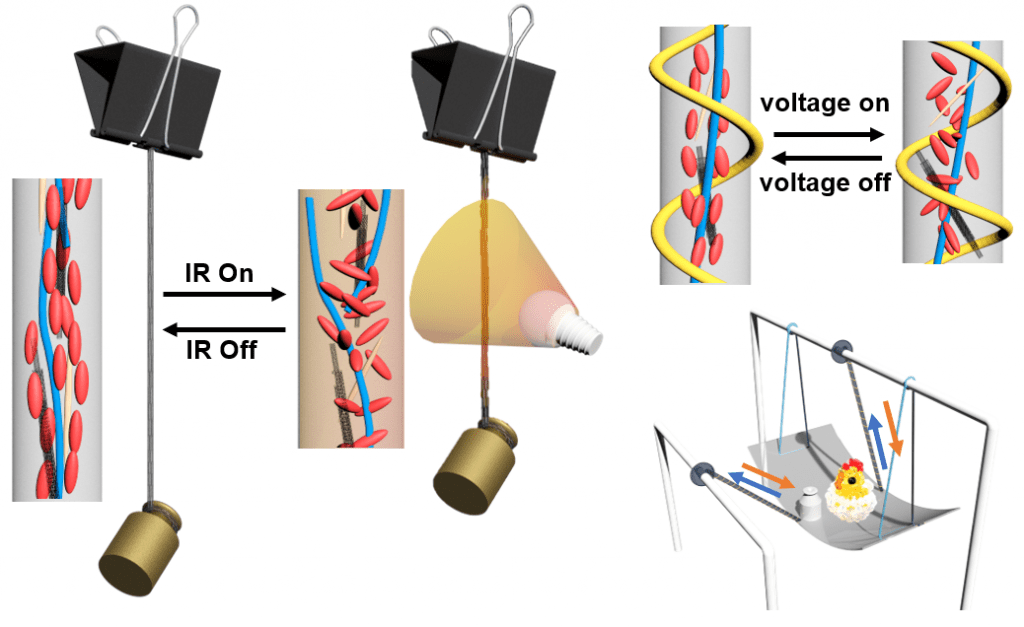
The filament can be placed into arbitrary patterns or integrated into system-level robotics for various types of locomotion. A maximum work capacity (the ability of actuators to perform mechanical work) of 38 Joules per kilogram is achieved, a value comparable to that of skeletal muscles in mammals.
“Our hybrid design of LCE filament allows the soft robots to lift heavy objects without diminishing their dexterity. The force generated during actuation is among the high values in the current soft actuators.” said Yuchong Gao, the lead author of the paper. “The muscle-like filament shape that offers one more degree of freedom compared to traditional film-based actuators is also ideal for the integration into diverse types of soft intelligent robotic systems.”
Kindly contributed by Jiaqi Liu, Ph.D. candidate in the Department of Materials Science and Engineering, University of Pennsylvania, USA.