This article is an invited piece from Professor Geoffrey Ozin, University of Toronto, and Jeffrey A. Herron and Christos T. Maravelias, University of Wisconsin-Madison, on the occasion of Professor Ozin’s birthday.
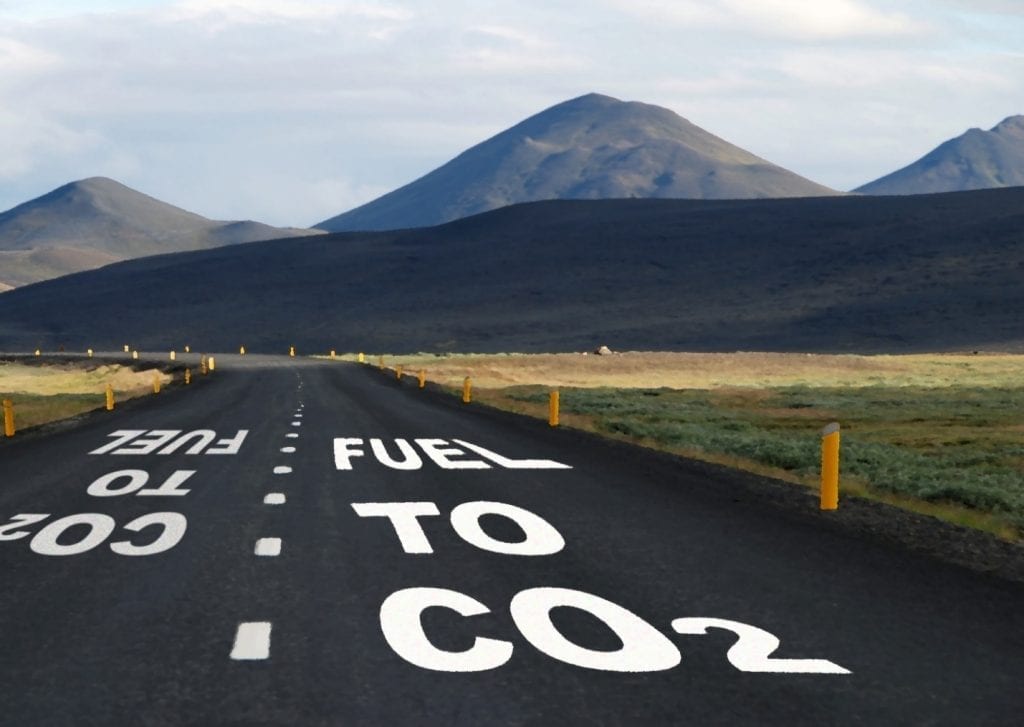
For the first time since the tracking of CO2 in our global atmosphere began, concentrations have reached a new record of 400 parts per million. In this article we imagine a world in which these anthropogenic CO2 emissions could be recycled back to a synthetic transportable fuel using only H2O and renewable forms of energy such as solar, wind and hydro power, in a carbon-neutral CO2-to-Fuel sustainable carbon-cycle. The race is on amongst materials chemists, scientists and engineers around the world to discover materials and processes that can enable this Utopian dream in the most energy efficient, environmentally responsible and cost effective way. Graphic illustration courtesy of Chenxi Qian.
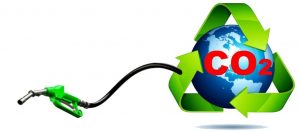
Priming the petrol pump with recycled CO2 from thin air
It’s ironic that after more than 40 years of globally competitive research on the conversion of CO2-to-Fuel, the first pilot demonstration to successfully take CO2 from thin air to the petrol pump turns out to be based on rather conventional materials and well established processing technology. In this article we ask if this impressive advance towards a decarbonized energy economy using recycled CO2 based fuels could provide a panacea to a carbon-neutral, climate-friendly, and environmentally-responsible global society, perhaps signaling the end of the road for unconventional rival approaches vying for a CO2-to-Fuel technology. For sure, the bold step of literally filling the tank of a car with fuel made from recycling the combustion product of fuel that can be produced at a price not too different to that obtained from legacy fossil resources is a monumental feat. It will definitely serve to catalyze materials science and engineering research aimed at improving the energy efficiency, expanding the scale, and decreasing the cost of the process, thereby throwing down the gauntlet as the CO2-to-Fuel technology to beat.
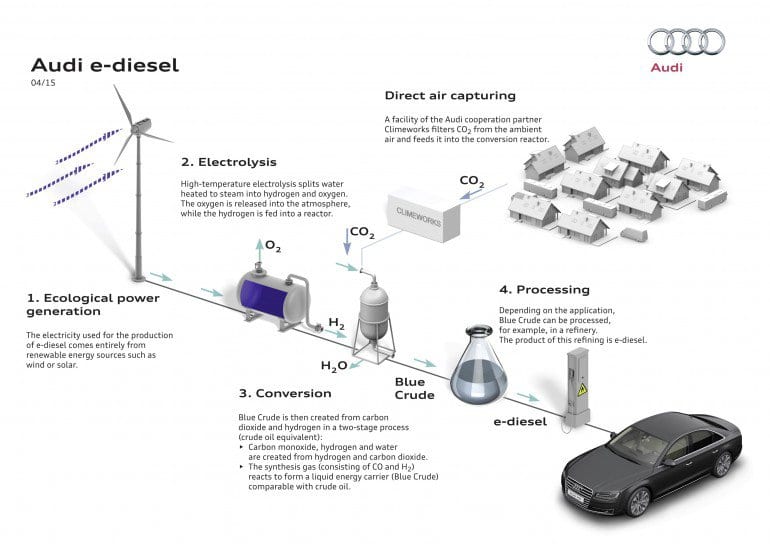
Figure 1: Audi process for producing diesel fuel from carbon dioxide. Image: Audi.
The stakes have been raised in the quest for a commercially viable CO2-to-Fuel technology with the recent announcement, by the Audi-Sunfire-Climeworks consortium of companies, operating in Germany and Switzerland, of a pilot project for producing diesel fuel from CO2 and H2O and renewable energy sources, such as wind or solar or hydro power. The CO2 supply was obtained mainly from a biogas plant supplemented with some CO2 captured directly from the air. While very few techno-economic details are currently available for an independent critical life-cycle-assessment, the publicized estimated price at the pump of 1-1.5 Euro/liter seems to make the future prospects for CO2-to-Diesel that is cost competitive with Fossil-to-Diesel a reality (see appraisal of this point below). A pilot plant in Dresden is destined in the months ahead to produce around 160 liters/day of the synthetic diesel, which they have dubbed “blue crude” [1].
The process employed for making “blue crude” depicted in Figure 1, and for the purpose of this discussion, actually involves five main steps: the first requires capture of CO2 from thin air; the second involves electricity generation from renewable sources; the third uses electrical energy to electrochemically split water into a hydrogen (H2) and oxygen (O2) mixture from which the H2 must be separated; the fourth uses this H2 to reduce the CO2 captured from the atmosphere, to form a mixture of carbon monoxide (CO) and water (H2O) in a high temperature and high pressure Reverse Water Gas Shift (RWGS) process, from which the H2O and unreacted CO2 is separated; and the fifth mixes the CO with the H2 to form synthesis gas (Syngas), which is subsequently converted in a high temperature and high pressure Fischer-Tropsch (F-T) catalytic procedure, to generate the long-chain hydrocarbons comprising the “blue crude”. To the best of our knowledge about 80% of the “blue crude” produced by the F-T process is suitable for synthetic diesel making is more analogous to crude oil where the other fraction is mainly lighter hydrocarbons which cannot be used in diesel fuel.
It appears that while the electrochemical, adsorption, separation and catalytic methods employed to make “blue crude” powered only by renewable energy sources are rather conventional in nature, the technology nevertheless works, can be scaled up, and has set today’s benchmark standard for converting CO2-to-Fuel. For any technology to compete commercially with “blue crude” technology, it will have to be more straightforward in materials and process engineering with less steps involved and more energy efficient and attractive economically.
Let’s consider some back of the envelope calculations for making “blue crude”: 1 kilogram of diesel contains 43.4 MJ of energy, so 1 liter corresponds to 36 MJ or 10 kWh, assuming diesel has a density of 0.83 kg/L. In order to get an order of magnitude estimate of the cost to make a liter of “blue crude” let’s assume that producing this amount of chemical energy requires an equal amount of electricity. Assuming that renewable electricity costs 3 times more than conventional electricity [2], one determines that the electricity to produce 1 liter of gasoline would cost 10 [kWh] * 3 * 0.05 [$/kWh] = $1.50 or 1.34 EUR.
Note that this is just the electricity for the electrolysis of H2O. It does not account for all remaining capital costs including CO2 capture, conversion and separation nor for the additional required energy inputs, such as, the electricity to compress captured CO2 for the RWGS and then the F-T reaction. This analysis suggests the cost estimate for a liter of “blue crude” is optimistic, if not unrealistic, at best.
Concerning the most promising alternative CO2-to-Fuel methodologies being explored today, it is worth stating at the outset that an energy conversion efficiency of less than 1% for the typical photosynthetic biomass process is unlikely to be a viable route for CO2-to-biofuels as it cannot be obviously scaled to satisfy future global energy demands and is most likely unable to impact greenhouse gas induced climate change, even if all the unused cultivatable land on earth was utilized. It seems that life cycle analysis of the material and energy balances of CO2-to-Fuel processes upon which the commercial success of biofuels spin-off companies ultimately depend, has caused many of them to falter as can be seen in the fading stock value (above) of some once-big-startups [3]. In a world that produces ethanol from corn and starch and biodiesel from soybean oil it is rather important to develop and commercialize advanced materials and catalytic processes that use CO2 and H2O as feedstock for making synthetic fuel.
That having been said, many people argue there will be no single renewable energy solution but a collection of solutions, each of which may be most viable to a specific location and environment. In this context, biofuels can play a role, especially in areas where crops such as sugar cane, which have photosynthetic conversion efficiencies up to ~6-8%, can be grown. Furthermore, even with low efficiencies the chemical energy can be regarded as free because nature has evolved to convert solar to chemical energy. So efficiency of biofuel production does not really impact capital cost as with other solar technologies where equipment has to be built to capture solar energy.
If not a biological approach for a viable CO2-to-Fuel technology, then what are the alternatives? Today, the main non-biological competitors are solar-powered photochemical, electrochemical, thermochemical and photothermal processes, the overall energy conversion efficiencies of which will determine the economics of the process [4 – 6].
In one route, akin to the “blue crude” process, CO2 is reduced by hydrogen, which is renewably produced by splitting water. Notably, there has been significant progress in technologies for water splitting, [7 – 10]. Though, in order for the production of H2 by the photochemical splitting of H2O using nanostructured catalysts to be cost competitive the materials and processes will require an improvement in efficiency by at least a factor of 100. Even if these efficiencies are achieved in practice it is not yet apparent that an aqueous phase solar powered water splitting process could be cost-effectively scaled up to handle globally significant quantities of H2 for a viable CO2-to-Fuel economy that could impact greenhouse gas climate change.
The same efficiency, scalability and cost considerations apply to aqueous phase photochemical conversion of CO2-to-Fuel where efficiencies seem to be stalled around 1%. By contrast, if the efficiency of a “tandem” gas-phase light-assisted heterogeneous catalytic process involving the splitting of H2O to H2 followed by the H2 reduction of CO2, operated under ambient conditions of temperature and pressure, could be improved by two orders of magnitude, it might become cost-competitive with “blue crude” technology.
In the case of H2 generation using photovoltaic powered water electrolysis systems, PV-EC, solar-to-fuel conversion efficiencies are moving beyond the US DOE target of 10%. This remarkable feat is being achieved by coupling high-performance low-cost silicon and lead iodide perovskite solar cells with water splitting catalysts, [11 – 13]. The H2 generated in this way can be transformed to electricity using fuel cells or converted to transportable liquid fuels by heterogeneous catalytic reduction CO2 via RWGS and F-T processes, where an efficiency of at least 10% is necessary for technologies of this kind to be commercialized. It is envisioned that similar accomplishments may be achieved using lead iodide perovskite solar cells in PV-EC configurations to drive solar conversions CO2-to-Fuels. However, as mentioned above, the cost of scaling up an aqueous phase solar-powered CO2-to-Fuel process will likely becomes prohibitive.
In this context it is noteworthy that in the solar-thermal (heat), photo-thermal (heat and light) and photo-chemical (light) approaches to the catalytic conversion of CO2-to-Fuel, the overall process is simplified as the electricity generation and electrolysis requirements of H2O splitting are side-stepped. Hence, with further optimization of the photochemical and thermochemical activity, selectivity and stability of materials and improvement of process efficiencies, the overall performance of solar-thermal, photo-thermal and photo-catalysis methods could be improved so that these methods become economically competitive with the “blue crude” technology. Though, even if the U.S. Department of Energy’s target cost of 2-4 $/kg of H2 is met, the cost of the renewable hydrogen to produce synthetic diesel is already ~0.65-1.30 $/L. A recent techno-economic analysis of photo-catalytic and photo-electrochemical water splitting systems calculated a price of 1.60-10.40 $/kg of H2, though there are still considerable engineering challenges to overcome [14].
Here it is worth noting that the solar-thermal method utilizes concentrated solar power to enable a high temperature (1000-2000°C) two-step metal oxide based redox conversion of CO2 + H2O into CO + H2 Syngas, which is subsequently processed to hydrocarbon fuels via conventional F-T heterogeneous catalysis. The most efficient solar thermal system reported to date involves the production of H2-CO Syngas using a two-step H2O-CO2 redox cycle. It is founded upon non-stoichiometric ceria and involves a high temperature reduction step operating around 1500°C, CeO2 -> CeO2-x + x/2O2 and low temperature re-oxidation steps occurring around 1000°C, CeO2-x + xH2O -> CeO2 + xH2 and CeO2-x + xCO2 -> CeO2 + xCO. This study utilized a 4-kW solar reactor converting CO2 to CO with rates of 0.5 mL CO per min per g catalyst, yields of 4 mL of CO per g catalyst per redox cycle, and, most importantly, solar-to-fuel energy conversion efficiencies that approach 4%. This method for producing Syngas has recently been integrated with storage, compression and F-T processing to form liquid hydrocarbons deemed suitable for commercial aviation. One only requires an improvement of 3-4 times for this CO2 + H2O to fuel process to become an economically competitive and industrially viable technology [15]. A major challenge however that still needs to be overcome with this approach is the thermal, chemical and mechanical stability of the metal oxide redox catalysts over many high temperature switching cycles.
It is possible that photo-thermal driven heterogeneous catalysis using both the heat and light of the sun could enable the conversion of CO2 + H2O or H2 to fuel under much milder conditions than currently employed in the solar-thermal method. Indeed, light-assistance of thermally allowed heterogeneous catalytic reactions is certainly an interesting opportunity and one that possibly could deliver a competitive CO2-to-Fuel technology with continued improvements in efficiency. As a scientific goal, the study of how light gets involved in photo-thermal heterogeneous catalysis is important and may end up providing clues that will ultimately enable the dream of gas-phase light-assisted high-efficiency conversion process of CO2 + H2O to a fuel such as CH4 or CH3OH to be realized in practice.
One way to transcend the complexity and efficiency of the multi-step Audi CO2 + H2O to fuel process is to discover a “dream” catalyst dubbed the “techno-leaf”, which is able to directly convert gaseous CO2 + H2O under mild conditions to a fuel, using just the energy contained in sunlight as the renewable power source. The gas-phase “techno-leaf” CO2 + H2O to fuel process, not to be confused with the aqueous phase “artificial leaf”, in essence combines steps 2 and 3 in the five step process described above with step 4 if we stop at CO and step 5 if we make fuels such as such as CH3OH, (CH3)2O, HCO2H or CH4.
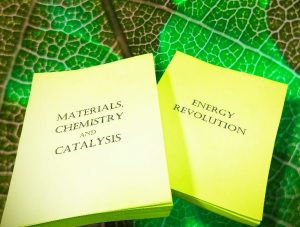
Figure 3: You can’t have an energy revolution without materials, chemistry and catalysis. Graphic image courtesy of Chenxi Qian.
If the “techno-leaf” could also capture CO2 and H2O from thin air and operate with low concentrations of CO2 in the presence of O2, like the “real leaf”, it is a very serious “dream” to combine all 5 steps of the above mentioned process in one operation. With revolutionary advances in materials, chemistry and catalysis to enhance the CO2-to-Fuel efficiency, this vision of the “techno-leaf” process could in principle be reduced to practice, Figure 3. This would be huge news, it would present serious competition to the leading Audi process in the race to implement a CO2-to-Fuel technology to enable an energy revolution and resolve greenhouse gas climate change.
In the case of a light-assisted process that converts CO2 and H2O to fuel, the water question is frequently asked. Conventional gasoline production requires roughly 3-7 liters of water per liter of fuel. Thus, the production of solar fuel is not expected to consume more water than the production of fossil fuel. One can argue that the required amounts of water can be provided by seawater desalination by reverse osmosis which is more energy efficient than extracting water from air by adsorption. The energy required for desalination is around 3-5 kWh per 1000 liters. The energy content of 1 liter of synthetic fuel is about 10 kWh. Thus, there are about three orders of magnitude between the energy required to desalinate water and the energy content of the fuel. This is entirely different to some biofuel paths, which require orders of magnitude more water to produce 1 liter of fuel. Then, water provision indeed becomes a problem, though this is, of course, dependent on the specific climate of the area.
Another pivotal concern is the carbon dioxide question, which relates to the most energy efficient and cost effective means of capturing and purifying CO2 for processing with H2O to synthetic fuels by any of the aforementioned methods. In the Audi process, much of its CO2 is captured from a concentrated stream from an industrial biogas plant, which is much more energy efficient than from the ambient air. In the short term, this makes practical and economic sense. Though for a long term sustainable solution, ideally, the co-extraction of CO2 and H2O from ambient air by a champion adsorbent would provide attractive logistical benefits for the production of synthetic fuels, especially in regions with limited or no fresh H2O resources. In this context, amine-functionalized cellulose fashioned in nano-fiber form has recently been identified as a promising sorbent that is able to concurrently extract CO2 and H2O vapor from ambient air with demonstrated potential for industrial scale applicability. The favorable adsorption and desorption capacities and energetics at low partial pressures, and tolerance to moisture in air bode well for the successful application of this CO2 and H2O co-extraction process. By combining this process with the conversion of CO2 and H2O to fuel, energy can be conserved and costs reduced because the need to transport CO2 and consume fresh water resources are eliminated [16].
It would be interesting to invent photoactive materials that can simultaneously capture CO2 and sunlight and convert the CO2-to-Fuel. This might be a way to reduce the entropic penalty pervasive in carbon capture and conversion processes. In a “one-step” solar-powered gas-phase CO2-to-CO “techno-leaf” the effluent of CO2 capture and conversion will have 80% N2, 20% O2, and a few ppm of CO2 and CO. Assuming 50% conversion, there will be, very roughly, 250 ppm CO2 and 150 ppm CO. This means that to get the product CO, it will have to be extracted from the mixture by a selective CO adsorbent. Currently, most research is targeted at CO2 separations, so although we only have one separation, designing materials that would extract CO from N2+O2+CO2 mixtures will be required. The alternative of removing N2, O2, and CO2 from the mixture is a prohibitive option because it would require the removal of huge amounts of gases and thus require a lot of energy compared to the production rate of the main product. Another approach is to capture CO2 and H2O on the photo-catalyst surface and convert the mixture to a liquid product, such as MeOH. One would still have to remove ppm amounts, but this time we have to separate a liquid product from a gaseous one, which can be done by simply cooling. In this case one would kill two birds with one stone, namely carry out separation and reaction in one step and have an easy separation for the final MeOH product.
Some final thoughts. Clearly companies like Toyota and Tesla have confidence in the future of the electric car. It’s true that renewable electricity with batteries is the simplest system, but batteries are costly, have limited range and take a long time to charge. But work is underway to address these limitations. Producing hydrogen and using it in a fuel cell is only a little more complex. But then you need a costly hydrogen infrastructure and good fuel cell performance. Despite millions spent by Ballard and other companies, fuel cells have not yet become competitive for vehicles. In this context, Audi’s blue crude involves the most complex processing, but produces a “drop in” diesel fuel replacement, requiring no new distribution infrastructure and no new vehicle design.
The outcome is not obvious. The good thing about the Audi process is that the companies Sunfire and Climbworks involved have taken the plunge and gone ahead with a pilot plant, which will stimulate lots of interest and no doubt some experience will be gained from this plus it will catalyze efforts by the materials researchers to work even harder to achieve the holy grail. However, we can’t really believe that the fairly conventional Audi process is the path to go along for conversion of CO2-to-Fuel in the long term.
- http://www.audi.com/corporate/en/corporate-responsibility/we-live-responsibility/product/synthetic-fuels-Audi-e-fuels.html.
- “Annual Energy Outlook 2015”, U.S. Energy Information Administration, Washington DC, 2015.
- http://www.economist.com/news/technology-quarterly/21584452-energy-technology-making-large-amounts-fuel-organic-matter-has-proved-be.
- Ozin, G.A., Energy and Environmental Science, DOI: 10.1039/c5ee00907c, (and references cited therein).
- Ozin, G.A., Advanced Materials, 2015, 27, 1957-1963; DOI: 10.1002/adma.201500116, (and references cited therein).
- Thomas, J.M., ChemSusChem., 2014, 7, 1801.
- Osterloh, F.E., Chemical Society Reviews, 2013, 42, 2294-2320.
- Tachibana, Y., Vayssieres, L., Durrant, J.R., Nature Photonics, 2012, 6, 511-518.
- Li, Z., Luo, W., Zhang, M., Feng, J., Zou, Z., Energy & Environmental Science, 2013, 6, 347-370.
- Hisatomi, T., Kubota, J., Domen, K., Chemical Society Reviews, 2014, 43, 7520-7535.
- Sabba, G,D., Kumar, M.H., Wong, L.H., Barber, J., Grätzel,, Mathews, N., Nano Letters, 2015, DOI: 10.1021/acs.nanolett.5b00616
- Cox, C.R., Leeb, J.Z., Nocera, D.G., Buonassisib, T., PNAS, 2014, 111, 14057-14061 (and references cited therein).
- Luo, J., Im, J.H., Mayer, M.T., Schreier, M., Nazeeruddin, M.K., Park, N.G., Tilley, S.D., Fan, H.J., Grätzel, M., Science 2014, 345, 1593-1596.
- Pinaud, B.A., Benck, J.D., Seitz, L.C., Forman, A.J., Chen, Z., Deutsch, T.G., James, B.D., Baum, K.N., Baum, G.N., Ardo, S., Wang, H., Miller, E., Jaramillo, T.F., Energy & Environmental Science, 2013, 6, 1983-2002.
- Marxer, D., Furler, P., Scheffe, J., Geerlings, H., Falter, C., Batteiger, V., Sizmann, A., Steinfeld, A., Energy and Fuels, DOI: 10.1021/acs.energyfuels.5b00351, (and references cited therein).
- Wurzbacher, J.A., Gebald, C., Piatkowski, C., Steinfeld, A., Environmental Science and Technology, Environmental Science and Technology, 2012, 46, 9191−9198; dx.doi.org/10.1021/es301953k, (and references cited therein).
Acknowledgments
GAO is Government of Canada Research Chair in Materials Chemistry and Nanochemistry. This work was supported by the Natural Sciences and Engineering Research Council of Canada (NSERC), the University of Toronto, Ontario Ministry of Research and Innovation (MRI) and the Ontario Ministry of Economic Development and Innovation (MEDI). The ideas and opinions expressed in this Perspective have benefitted enormously from the critical reading, insightful feedback and writing skills of Sir John Thomas, Aldo Steinfeld, Andreas Sizmann, Valentin Batteiger, Erik Haites, Bettina Lotsch, Moti Herskowitz and Bob Davies.