The steel sector accounts for 6.7% of the world’s CO2 emissions, and is the second-largest industrial user of energy, consuming 2.6×107 TJ in 2007. Reduction in energy use and CO2 emissions in the steel industry is rapidly reaching the limits defined by the laws of physics and chemistry. To combat this problem, a flash technique has been conceived as a novel ironmaking technology by Sohn at the University of Utah.
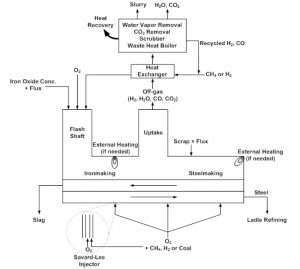
A schematic diagram of the novel flash ironmaking process.
It is based on the direct reduction of iron ore concentrate particles using a gas such as hydrogen or natural gas. This process will bypass pelletization and avoid the need for coke, which will make it an ecofriendly and less energy consuming technology compared to the blast furnace. Another potential benefit of this process is the possibility of steelmaking in a single continuous process, as shown in the schematic.
This research has also determined, for the first time, the effect of water vapor on the distribution of Mn between slag and molten iron. The distribution ratio of Mn under H2 and natural gas conditions is 29 and 43% less than under the CO/CO2 atmosphere. However, based on materials balance, the novel flash ironmaking technology is expected to produce iron with a lower Mn content (~0.1-0.2 wt%) than the blast furnace pig iron, which typically contains 0.9–2.5 wt% Mn.